Connor Weller got his start making and selling 3D-printed cookie cutters on his college campus.
When the coronavirus pandemic reached the Northwest and area hospitals faced a shortage of personal protective equipment, the Washington State University student paused his startup plans and pivoted to 3D-printing PPEs on a pro-bono, volunteer basis.
“All the machines are being run for printing specifically PPE. Because that's where it's needed, and I can help.”
‘Over 1 Year Of 3D Printer Time’
More than 9,000 health-care workers in the U.S. have been sickened by the SARS-CoV-2 virus, recent CDC data shows.
Across the Portland area, infection rates among nurses have been rising in some hot spots, with other health care providers resorting to wearing swim goggles in lieu of face shields.
That’s where makers like Weller come in. In his Vancouver, Washington, home office, four 3D printer heads are constantly on the move—printing face shields at a rate of one every 1 to 2 hours during OPB’s visit.
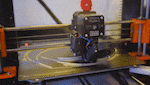
Connor Weller's PRUSA machines printing RC3 face shield parts, a design that was verified by the Czech Ministry of Health. Arya Surowidjojo/OPB
His setup is just one production line within a crowdfunded network of about 200 volunteer 3D print makers, named MakerForce, that Weller himself spearheads with Shashi Jain. Jain is an Intel innovation manager who also organizes the Portland 3D Printing Lab meetup.
“Our group thinks of itself as a manufacturing emergency response team,” Jain said. “We're popping up to manufacture things that fill this gap before the traditional supply chain can take over.”
By Jain’s count, MakerForce and its allies have delivered 1,516 face shields, 3,850 eye shields, 200 ear savers and 50 sewn masks between late March, when production began, and April 17.
“We've achieved over 9,000 print hours in 22 days. That's over one year of 3D printer time.”
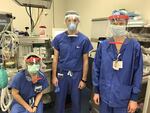
Health care workers at Providence Health wearing 3D printed face shields manufactured and donated by local makers.
Courtesy of MakerForce / Portland 3D Printing Lab
The speed of this grassroots 3D printing response is in large part due to its supply chain management, all done through the MakerForce website. “It's meant to be really simple. You got a 3D printer, you can help right away,” Weller said.
Makers of compatible skill sets can sign up online as volunteer suppliers and claim PPE manufacturing requests that best suit their capacities.
MakerForce instructs all volunteers to sanitize all finished PPEs before they're put in plastic bags, and hospitals later go through another cleaning process with specialized equipment, Jain said.
The organizers have also partnered with Vancouver-based ProtoPlant, which manufactures filament, so that 3D print makers don't have to pay out of pocket for their raw materials.
On the demand side, MakerForce's website allows hospitals and physicians to view a catalog of available PPE for manufacture and how the designs have been verified as safe to use in medical settings.
“There's a trust element that we have to bake into the whole process,” Jain said. “We're working with designs that are verified by other hospital systems, whether it be a European hospital system, OHSU (Oregon Health and Science University) or something in between.”
The bulk of Weller's print jobs, for example, are the Prusa RC3 face shield that was verified by the Czech Ministry of Health and a sturdier NIH PRUSA Remix that was approved by the U.S. Department of Health and Human Services (NIH)—both designs were released under an open-source license.
Local Pop-Up Supply Chains
This local manufacturing of PPEs approach has now become a critical part of the global pandemic response, from Australia to Tunisia.
And it’s not restricted to just home and hobby makers. Design and manufacturing companies equipped with 3D printers have also joined the volunteer movement.
Sigma Design, an engineering consulting firm in Camas, Washington, has used design files released by HP to rapidly spin up production of emergency PPEs.
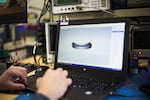
Sigma Design test lab manager Douglas Burnette previews HP’s 3D face shield design, April 6, 2020.
Arya Surowidjojo/OPB
“The timeline of a week from proposal to pretty much starting mass production was probably a little tighter than we would usually take on. But this was right up our alley to be able to do quickly,” said Sigma Design test lab manager Douglas Burnette.
By Burnette’s count, the firm has manufactured and donated around 1,200 PPE items to more than a dozen facilities throughout the Portland metro region.
Despite the efficacy of these pop-up supply chains, both Sigma Design and MakerForce acknowledge that their efforts represent an interim solution for the PPE shortage crisis.
Traditional PPE mass manufacturing is typically done through a process called injection molding, which normally takes 8–14 weeks to design, machine mold, test and deploy for volume production, Burnette said.
Although the 3D printing method can take as little as a single day to spool up, a factory injection molding machine can make one face shield per second once calibrated, compared to the 1–2 hours timeline for a 3D printer.
“3D printers really shine when they can make a lot of different things, and not so much when they have to make the same part over and over,” Connor Weller said.
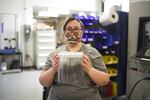
Evelyn Verzwyvelt, design for manufacturing lead at Sigma Design in Camas, Washington, holds up an assembled face shield prior to sanitizing, April 6, 2020.
Arya Surowidjojo/OPB
The longer the coronavirus pandemic continues, however, and without significant reforms made to improve the vulnerabilities of the global supply chain, innovators like Jain believe the 3D printing space will continue to evolve and play host to new solutions.
“Our PPE is meant to be a stop-gap. Could it be more? Perhaps. We're writing the story of local pop-up supply chains as we go.”
OPB reporters and photographers are capturing “Postcards from the Pandemic” to document the lived experience of people in the Northwest during this historic and unusual time.
We want to hear your experience, too. You can send us a voice memo by email to postcards@opb.org. And be sure to include your phone number.