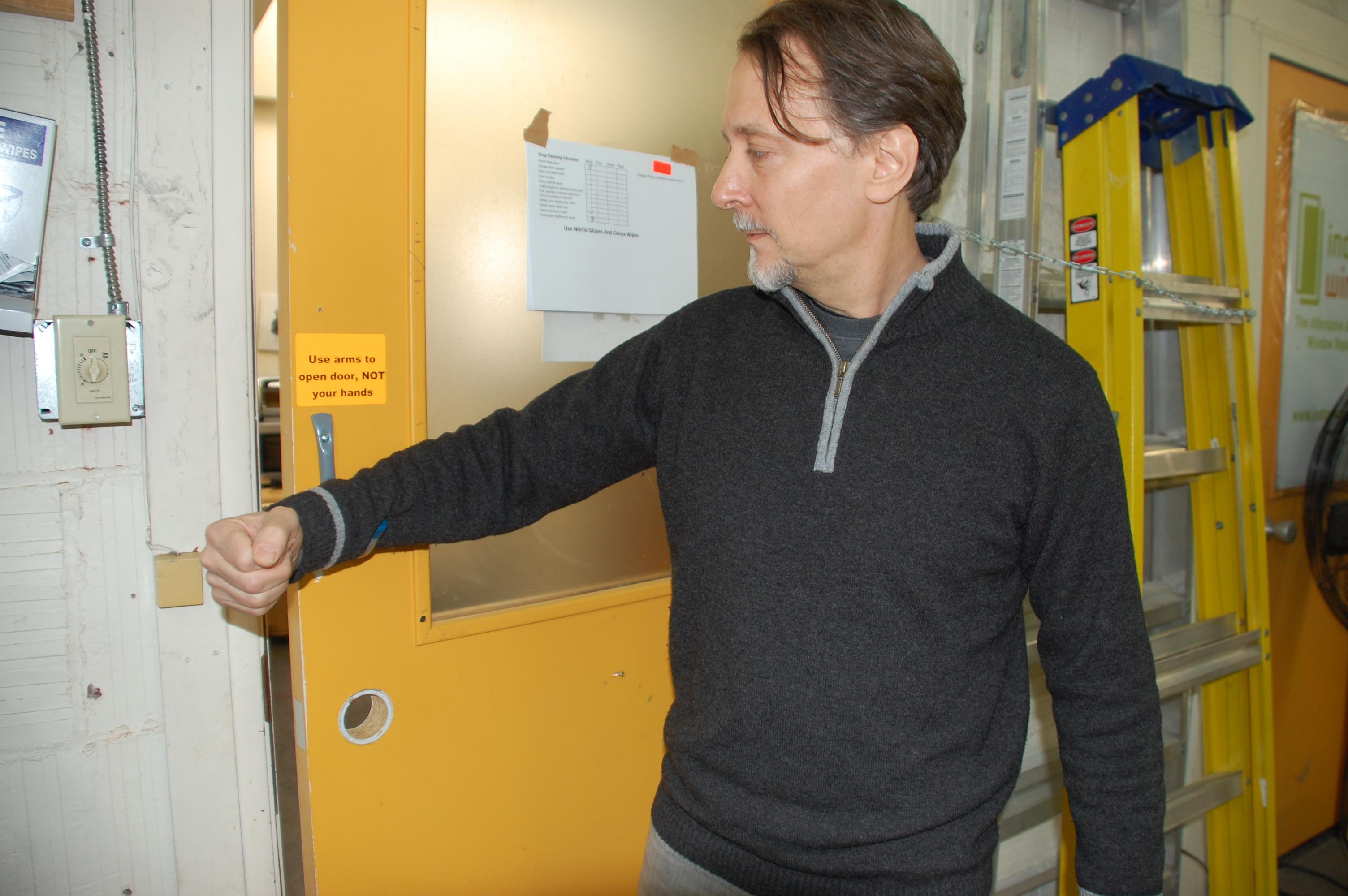
Coronavirus adaptation: Indow CEO Sam Pardue demonstrates how to pull the factory door open with an elbow. "We don’t want people using doorknobs anymore at all," he said.
Kate Davidson/OPB
Don't bother reaching for the doorknob at Indow, a Portland company that makes energy-efficient window inserts.
Chances are it’s not there.
The handles of the company refrigerator have also been pulled off. They’re propped unceremoniously against the wall.
These small changes are part of one small business's response to an existential threat: the coronavirus pandemic that's ravaging the economy, shuttering bars and restaurants and destroying American jobs.
Most of Indow’s employees are now working from home, but that’s not an option for the people who make the product the company sells. It’s a dilemma that much bigger factories across the country also face.
“Factories have got to stay in operation or the economy’s just gonna be done. It’ll be a depression,” said Sam Pardue, Indow’s founder and CEO. “So how can we have factories in operation, but still have the workers safe?”
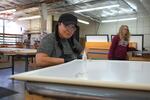
Melanie Baca helps produce window inserts at the Portland company Indow on March 16, 2020. Most employees started working from home during the coronavirus pandemic, but the factory workers can't do that.
Kate Davidson/OPB
Pardue is not a public health expert, so he turned to what he knows. He decided to employ the principles of “lean manufacturing” to try to reduce the risk of coronavirus transmission at work.
“Lean” is a system for reducing waste and inefficiency, famously used by the Japanese car maker Toyota. It’s such a bedrock part of contemporary manufacturing that it’s almost a way of life.
So, on the morning of Monday, March 2, Pardue organized Indow’s first “gemba walk,” a tool of lean manufacturing. Oregon had just announced its first COVID-19 case the Friday before.
A gemba walk is when teams of people walk a shop floor to observe the flow of work and identify inefficiencies. In this case, the teams identified a different issue: the toaster oven.
“We took the gemba walk concept and we’ve walked through the factory to identify places where people touch surfaces with their hands — multiple times per day, multiple people,” Pardue said.
Many of those surfaces now have brightly colored stickers, so they’re not missed during cleaning. The stickers were inspired by another concept in lean: visual factory. If you make a system easy to see, you get reliable and repeatable results.
A later gemba walk led to “engineered changes” such as removing some doorknobs (and installing elbow hooks), ditching the fridge handles (and adding a foot pull) and even McGyvering the toilet (see photo).
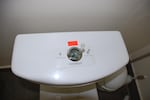
Coronavirus adaptation: Indow altered the company toilet so employees don't have to flush with a finger anymore. Now, they can push with a forearm.
Kate Davidson/OPB
Pardue said removing doorknobs draws on another principle of lean manufacturing: “poka-yoke” or mistake-proofing. That’s when you make it impossible to attach or use a part in the wrong way.
“We’re eliminating the opportunity for somebody to go through this door incorrectly,” he said. “Because we don’t want people using doorknobs anymore at all.”
To Pardue, his company’s coronavirus plan is more than a glorified cleaning routine. It’s meant to engender trust at a time of fear. He’s encouraged sick people to stay home and committed to loan an additional two weeks of paid time off to employees recovering from a respiratory illness. That’s made production workers like David Springer feel safer continuing to work.
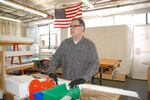
David Springer helps assemble energy efficient window inserts at the Portland company Indow on March 16, 2020. "A lot of the office people aren't here," he said, "But we have to be here to make the product."
Kate Davidson/OPB
“I have a 6-month-old baby, so I am concerned at times, but also trying to figure out how to continue to move,” he said. “A lot of the office people aren’t here. But we have to be here to make the product.”
Social distancing is part of Indow’s plan. The production workers are already fairly spread out on two factory floors, though they do cross each other’s paths. The company added a second break table as well.
Still, the 15 manufacturing employees at Indow are a far cry from the massive numbers of people who work for manufacturers like Boeing, which has already experienced COVID-19 in its ranks. It's unclear whether the small manufacturer would stay open under a shelter-in-place directive.
In the end, the principles of lean manufacturing can’t stop a pandemic. They can’t control whether there’s a recession that dries up business. But in Portland, they have provided a coping template for one small business hoping to weather the turbulent months ahead.
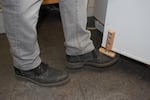
Coronavirus adaptation: Indow pulled the handles off the company fridge and installed this foot pedal instead.
Kate Davidson/OPB