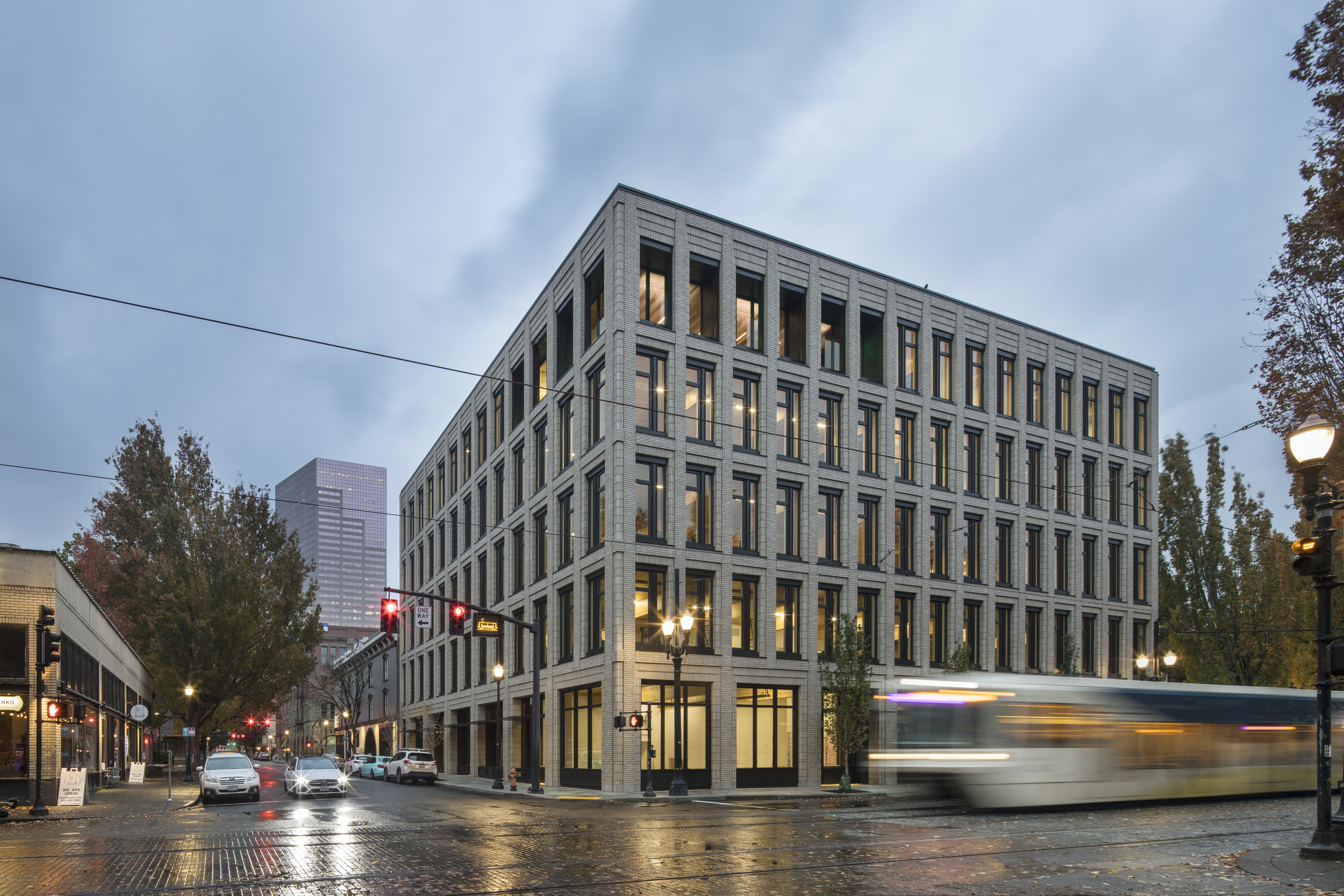
In May 2024, the PAE Living Building in Portland's Old Town neighborhood was certified as a Living Building after it met a rigorous set of sustainability requirements, including generating more energy than it uses and capturing rainwater for all its water needs. There are only 36 certified Living Buildings in the world, including three in Oregon.
Lara Swimmer
Last month, a 5-story commercial building in Portland’s Old Town historic district was awarded one of the most rigorous sustainability certifications in the world, given by the Portland-based International Living Futures Institute. There are only three dozen certified Living Buildings in the world, and the Portland building is the first commercial one to achieve it. Living Buildings must meet a range of strict requirements, from the design to operation. That includes using renewables like solar power to generate at least 5% more energy than is needed and harvesting rainwater to supply all the water for drinking and other uses.
The PAE Living Building at SW Pine and 1st Ave. not only met these standards but went one step further by being engineered to last at least 500 years to withstand a massive Cascadia Subduction Zone earthquake. Kathy Berg is an architect and partner at ZGF Architects and the project lead. Paul Schwer is the president emeritus of PAE, an engineering firm that co-owns, along with ZGF Architects, the PAE Living Building and is headquartered inside it. They join us to talk about their collaboration on the space, and why they hope it could be a model for commercial developments elsewhere.
The following transcript was created by a computer and edited by a volunteer:
Dave Miller: This is Think Out Loud on OPB. I’m Dave Miller. Last month, the five-story commercial building in Portland’s Old Town was awarded one of the most rigorous sustainability certifications there is. The PAE headquarters building is officially a Living Building – one of only about three dozen in the world. Living Buildings have to meet a range of strict requirements from design to operation. This one generates more energy than it uses, it relies only on rain water, and it creates marketable fertilizer and compost out of its liquid and solid human waste. It was also engineered to last at least 500 years, meaning it is expected to withstand the massive Cascadia Subduction Zone earthquake. Kathy Berg is an architect at ZGF Architects and the partner in charge of this project. Paul Schwer is the president emeritus of PAE, the engineering firm that commissioned this building. They both join me now. Congratulations and thanks for coming in.
Paul Schwer: Thank you.
Kathy Berg: Thank you.
Miller: Kathy Berg, first. What is the big idea behind the Living Building Challenge?
Berg: The Living Building Challenge is basically a process that a building can go through to prove that it is self-reliant, I guess in a way you could say. There’s seven different “petals” that you seek to achieve. And if you think of it as a tree on the side of a mountain – which is a comparison Paul loves to use – the tree can only use the resources that fall upon it. So the sunshine from the sky, the water falling on the soil around it, the nutrients from the soil. We think about a building in the same way; it can use the solar resource or geothermal resources for energy. It needs to use the water that’s falling on it for the occupants’ needs. And then there’s several other “petals” that relate to beauty, and equity, and sight that we’re working to achieve when we pursue a Living Building.
Miller: Paul, can you describe just what it’s like to be in the building?
Schwer: Yeah, it’s interesting, Dave, because the building feels different when you’re in it. It feels – one, it’s beautifully day-lit, and then it’s a CLT (cross-laminated timber) wood building. So you’re surrounded by wood in the ceiling which really feels very, almost homey, not like an office building. In addition, it’s heated with a radiant floor heating and cooling system. So we have people take off their shoes in the office and wander around in their socks.
Miller: Wait, radiant cooling? Because I know radiant heating, and it’s a delightful feeling.
Schwer: Exactly.
Miller: And you can use the same coils under a floor and put cold liquid through them?
Schwer: Exactly. So, a heat pump can either produce hot water, which we do in the winter time, or cold water, which we do in the summertime. So, in the summer we run cool water through the floor – not as cold that it would condense the moisture in the air, but cool enough that it cools the building. So what happens in a building like that is your body doesn’t need to radiate a lot of heat out. So you feel comfortable at a much wider temperature range than you would in a building that had just an air conditioning system using air.
Miller: You’re describing what sounds like a pleasant building to be in. If I didn’t know that it was a Living Building, would anything tip me off or would I just think this is a pleasant place to be?
Schwer: Nothing would tip you off directly, no. And the building was built in a historic area. So, some of the buildings have PV [photovoltaic] panels that you can see from the street and they might say, “Oh, that’s a building powered by solar panels.” But you can’t see any of that in this building, so there’s nothing that would tip you off. You’re in a classy office building that feels really comfortable.
Miller: I mentioned that it creates more energy, electricity than it uses. Kathy, it’s relatively common now for buildings to have solar panels. It’s less common for them to process human waste into liquid fertilizer or compost. Can you describe how that system works?
Berg: Sure. The first step in the process is somebody’s using a facility. And, if you can imagine a similar toilet to what you would see on an airplane, it is a vacuum flush toilet that takes the waste from the human down to the first floor mechanical room, using as little water as possible.
Miller: Is it as loud as an airplane toilet?
Berg: No, I don’t think so.
Miller: That can be shockingly loud.
Schwer: No, not that loud.
Berg: Definitely not that loud. Much more suited for a building. Once it’s down there, if it is liquid waste, we have a way to take that to a distillation column that turns that into fertilizer that you can use on your lawn or garden; that is actually sold in local nurseries. If it is solid waste, it goes to a series of composters, which are big blue boxes that are filled with that compost and then mixed with organic materials to turn that into a compost that can be again, used as a fertilizer.
Miller: Paul, your engineering firm was involved with building a Living Building in Seattle in the past. What did you learn from that experience that informed the way you approached this one?
Schwer: Yeah, it was interesting. That building was the Bullitt Center, built for the Bullitt Foundation. And the system that Kathy just described, that was one of the big lessons learned, because on that building, we actually had to tear out the composting system. And what we didn’t realize, Dave, is that people have their favorite toilet. So in that case, each toilet went to one composting bin, so one would fill up or one would fill with liquid. This one we separated, we have waterless urinals, so we separate the urine to turn it into fertilizer, and then we’re able to move the composting around.
So, literally a mechanical system in that building that failed helped make this building successful. That’s one of the things about these buildings is pushing kind of the cutting edge or the bleeding edge so that the mistakes we make others can learn. Kathy and I just got back from giving a talk in Atlanta, and the whole purpose of the talk was all the things that we learned in designing these buildings.
Miller: When I think about engineers or engineering firms – and maybe this is my own failure of understanding of the job that you do – but I think about the architecture design folks, they have drawings, they say, “This is what we want it to look like and feel like.” And then engineers make sure that it’ll work structurally, that it’ll be sound, that the beams will support the weight, etcetera. Did you have a bigger role in the design of this building since it was going to be your headquarters since you commissioned it?
Schwer: Well, not just in this building, but every building is much more collaborative. The days of a lone architect and everyone else responding to that are past, and ZGF especially is a very collaborative firm. So it’s not just the structural engineers that design the beams and the columns, but the mechanical engineers that design the heating and cooling system, the electrical engineers that design the battery systems and the micro grids, the telecommunication engineers. There’s a whole bunch of different engineers involved with the process, but it’s really an integrated team. If you had sat in a meeting on that building, you probably wouldn’t be able to tell who was the architect and who was the engineer because everyone is talking about all aspects of it.
Miller: The Living Building certification did not require you to build a project that is expected to last 500 years or more. But you did. Kathy, why did you take on that extra challenge?
Berg: You know, I think it was really well said by our structural engineer on this project. She grew up in Europe and said, “We don’t design buildings there to last for 50 years as you do often in this country.” It makes much more sense to try to design a building that’s gonna last longer; it’s more sustainable. And so we really started with that mindset. Paul and I have been kibitzing back and forth on this over pizza and beer and talking about what does it take to make a 500-year building? And the structural system was that first element. How do we design a structural system that can last that long? And this mass timber structure that we have, we do really believe it will last 500 years.
Schwer: Yeah. So we started with design, so you have to have a well-designed building; we checked that box, we felt. Then you have to have a building that is really well built. So we hired Walsh Construction, a great local firm who really understands building the skin of the building, the building envelope, things that are gonna last the longest part of the building, and they’re very, very good at that. So if you have a good design, a good structure, a good contractor, those are the first two things you need. And then what else do we come up with, Kathy?
Berg: We focused a lot on, what will the maintenance of the building be over time? So we’re not suggesting that this will be its building, this building will be exactly the same in 500 years. The roof will need to be replaced, some of the equipment will be replaced. But we thought about how do we select materials that will last a long time and be easy to maintain. So we have brick on the facade. We have double pane fiberglass windows. We have a really solid exterior envelope, that if it’s well-maintained, should last 500 years.
Schwer: And then it has to make it through the Cascadia event, right? Because when we hit that point and I asked Anne, our structural engineer, I said, what happens? And originally, we’re just building this building to code, and she assured me that all the people would get out safely. And of course, I was concerned about that, Dave. And then I turned to her and said, but what about my building? And she said, “Oh, it’ll be a total loss.” And I said, “Well, that’s not gonna make our 500 years. We have to make it through that earthquake.”
And we were designing our building to be about eight inches away from the Pine Street Market, which many people might be familiar with. And I asked Anne, if we stiffened up our building, could we build it closer? So she did a bunch of calculations and we built it four inches closer to the Pine Street Market, and that added 200 square feet of rentable area – because it was four inches times five stories, times two sides of the building. That added enough extra rent to pay for the extra structure. So we are in a, what’s known as a category four seismic building – the same as a hospital, the same as a fire station, and we’re just a commercial office building.
Miller: That is an excellent example of the push and pull of design elements – in this case, seismic resilience. How much it’s going to cost to do that, and then is it going to pencil-out in terms of your investors. Because it seems like a key point here is this is not a publicly financed building. This is just a regular old commercial investment with a lot of debt, the way real estate developers liked to work. So what did that mean in terms of the decisions you had to make, that this was traditionally financed?
Schwer: Yeah. One thing, the last thing I wanted to end up on the 500 year building is we came up with, the last thing the building has to be is loved. If the building is not loved and cared for, it’s not gonna last 500 years.
Miller: Nothing does if it’s not loved.
Schwer: Exactly. So we’re hoping it’s loved. But one of the real reasons we designed this particular building was no one had designed a commercial office building to meet the standard. So it was an extra level of degree of difficulty, and we wanted to meet that because if it exists, it’s possible. A lot of your listeners probably may know who Roger Bannister is. Does that name ring a bell with you?
Miller: He was the first one to run a sub-four-minute mile.
Schwer: Exactly. So, in 1896 the Olympics came back. That was the race to beat. No one thought it could be done. By the 1950s, there were literally papers being written; it’s physiologically impossible. So he broke it. Do you know how long his record lasted?
Miller: I don’t
Schwer: Forty-five days. So the reason it was broken 45 days later is because people believed it was possible. People feel, on our building, a commercial building built within an investor-led development team could never meet these standards. So we wanted to prove that it could be done, and now it exists. Therefore, it’s possible. So we’re hoping now other developers looked at this and we’ve had 3,500 people tour the building – even during COVID – to see how did you pull it off?
Berg: And we’re actually seeing that come to fruition already. We had a client of ours, who was considering doing a black water wastewater treatment, tour the building. They were really unsure about it. Once they saw it in place, they came back and were much more interested in pursuing it. So seeing is believing.
Miller: But I mean, what does it tell you that there are only a few dozen certified Living Buildings around the world since this program has been up and running for more than a decade now? I mean, if the basic idea here is, if people see it, then they’ll replicate it. That relatively small number makes it seem that the full replication hasn’t happened on a grand scale yet.
Schwer: Correct. And this is the first one that’s actually designed to make a profit. So we’re just beginning that trend now, Dave, with this building. The other buildings were more for foundations, or universities, and that kind of thing. It is a challenge, and the building industry is very conservative for a reason. I mean, they’re very expensive to build. If you make a mistake on it, they’re hard to fix. The mistakes are hard to fix. So it’s a very risk-averse industry, and by having a few buildings trying to go out there, we’re trying to show that it can be done. But yeah, it’s slow-going right now.
Berg: I would just add that just because this was the 35th fully certified Living Building, even if you don’t go fully Living Building, if this helps somebody take a step to do one of the systems that we included – maybe you’re just zero water, right? So this is its own water district, all the water that falls on the roof we drink in the building. Maybe you’re just net zero energy, maybe you just deal with waste; if you do one of those things, that is better than what most commercial office buildings are doing right now. And if it can motivate people to do that, we’re headed at least in the right direction.
Miller: You’d mentioned that the two of you recently took part in a kind of lessons-learned talk. Kathy, what’s one of the big lessons for you? Something that, in a sense we’re saying, what would you do differently? What would you recommend that people do differently if they want to try to emulate this model? What’s number one for you? Number one today.
Berg: Number one today is to put the right team in the room – and we had it on this building. But I think it is sometimes overlooked when we’re going into these design exercises, that we had the developer, we had the contractor, we had all of the engineering team, we had the architect at the table with a common mission very much aligned. And that was the key to so many of the moments when we got to a difficult decision or a hurdle we had to make it across; it was having everybody in the room at the same time. The answer to a problem didn’t always come from the person you thought it would. And that’s what allowed us to get this built
Schwer: And we were all investors too. And that made a difference because normally in a commercial office building, we’re given a construction budget to hit, right? And that’s what we shoot for, right? But we don’t see the other side of the real estate proforma. We don’t see how rent’s affected, a rentable area, all these things that we were relatively new learning about. And one of the things there, that’s how the seismic thing correction or design help was, was knowing the other side of the real estate proforma. So that’s I think really important piece.
Miller: You had financial skin in the game.
Schwer:Yeah. But even if we didn’t, we now understand it in a different way. So when we do our next building, even if we don’t have skin in the game, we’ll understand that in a fundamentally different way.
Miller: One of the Living Beauty standards in the manual is about beauty. It says, “The project must contain design features intended solely for human delight and the celebration of culture, spirit and place appropriate to its function.” Kathy, what’s a feature that is just for human delight?
Berg: My favorite moment is when you walk into the ground level of the building. We have an art piece by Toma Villa, a large wooden coin about 8 feet across in diameter carved to talk about the history of the site and what the winds of the Columbia meant. It is a beautiful piece that really harkens back to people that first lived on these lands. And I find it to be both a meaningful and a beautiful moment when you walk in the building. And that was something that PAE felt was important to commission as a visual land acknowledgment.
Miller: Paul, do you have a favorite space?
Schwer: Oh, yeah. It’s the Deckony, which is a combination of the word deck and balcony that was invented by Kathy right here – new word in the English language. And we knew it would be a great space because the windows completely open, they fold back so it feels like you’re outdoors when you’re on the corner of the fifth floor. And we knew it would be a special space for our staff. But what I didn’t anticipate is we have literally had hundreds of events there – non-PAE events – nonprofits using that space, professional organizations, the AIA, other groups come in to use that space. So it’s become like a community gathering space because it’s such a special space. We have an event there tonight and tomorrow night.
Miller: Paul and Kathy, thanks very much.
Schwer: Thank you.
Berg: Thank you.
Miller: Paul Schwer is president emeritus of the engineering firm, PAE. Kathy Berg is an architect and partner at ZGF Architects, the partner in charge of this Living Building certified building in Old Town in Portland.
Contact “Think Out Loud®”
If you’d like to comment on any of the topics in this show or suggest a topic of your own, please get in touch with us on Facebook, send an email to thinkoutloud@opb.org, or you can leave a voicemail for us at 503-293-1983. The call-in phone number during the noon hour is 888-665-5865.