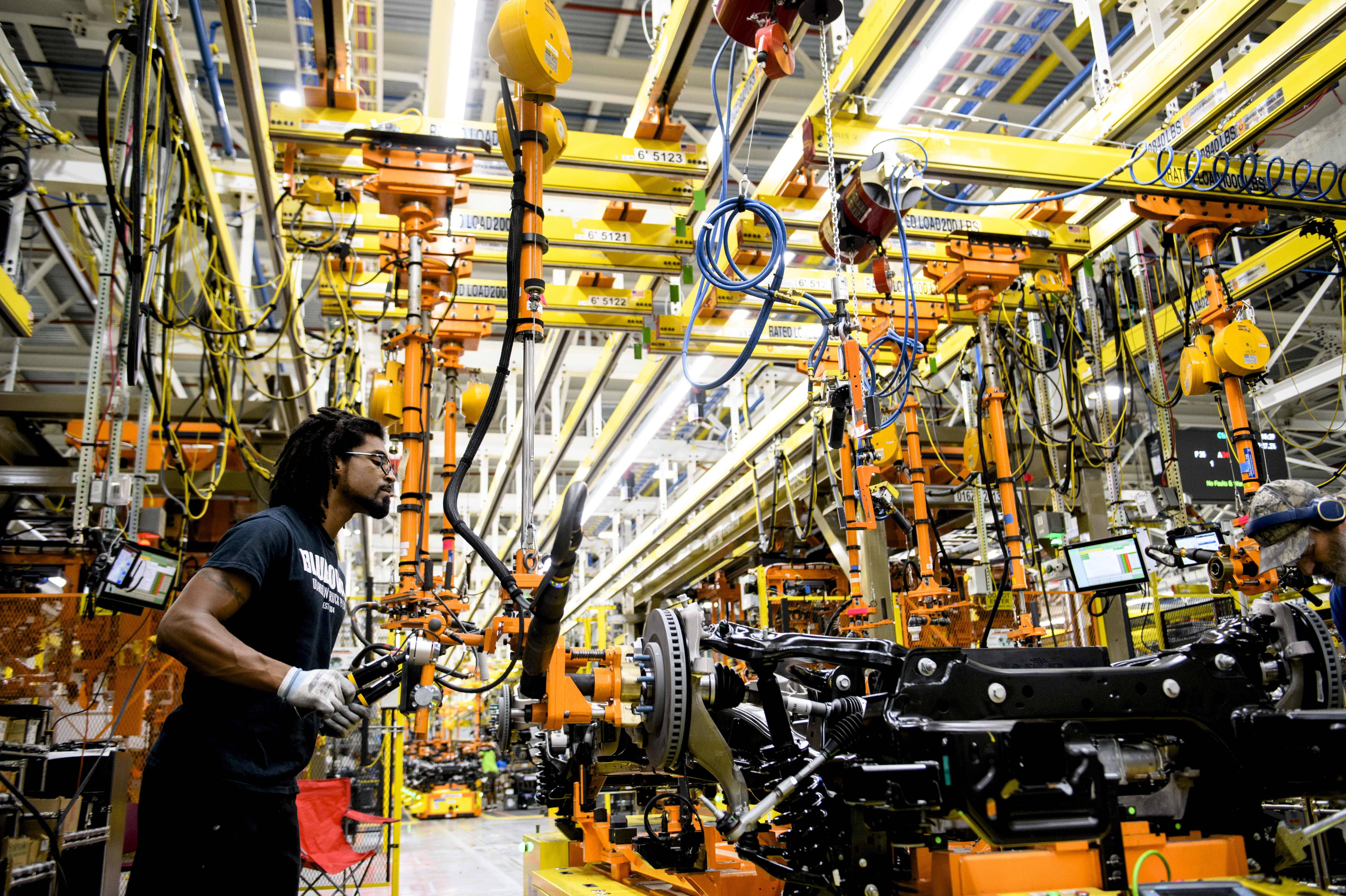
Jaylin Jones, 28, an assembly floor technician, while working on the assembly line at the Ford Rouge Electric Vehicle Center in Dearborn, Mich., on Sept. 7, 2022.
Brittany Greeson for NPR
The work weeks are long and exhausting for 28-year-old assembly line worker Jaylin Jones.
For 11 hours a day, sometimes six days a week, Jones and a couple hundred other workers race to assemble Ford’s slick new pick-up truck known as the Lightning.
"It's always busy in here," says Jones, who spent years working on the gas-powered F-150 and was recently retrained to work on its electric counterpart. "High demand, so we got to put them out."
So many customers placed initial orders for the Lightning, Ford hit its production capacity and stopped taking reservations for a while. To meet the skyrocketing demand, the company has been retraining many of its gas-powered assembly line workers and transferring them to the electric plant, which Ford is currently expanding to double in size.
What was a niche option in the auto market just a few years ago is quickly becoming the car of choice among many buyers. Car companies are shifting their resources to expand their electric fleets, a process that will significantly impact the auto workforce, from blue-collar workers to engineers who have devoted their careers to developing gas engines and transmission.
"I'm worried about how do we get enough people here, how do we fully train them," says Chris Skaggs, who is in charge of scaling up operations at Ford's electric plant. "Some people pick it up more quickly, some people pick it up a little bit slower."
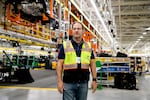
Ford Plant Manager Chris Skaggs at the Ford Rouge Electric Vehicle Center in Dearborn, Mich., on Sept. 7, 2022.
Brittany Greeson for NPR
Making electric cars means fewer parts, more automation and different types of engineers
New registrations for electric vehicles in the United States have grown more than 250% over the last five years, according to credit-reporting company Experian. In China, electric-car sales nearly tripled last year to 3.3 million, making up about half the global total, according to the International Energy Agency. Certain states, like California and New York, have announced plans to phase out gas cars by 2035.
These vehicles have fewer parts, and making them will eventually require fewer workers. On top of that, the auto industry for years has been moving toward increased automation.
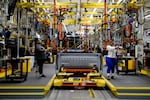
Employee work on a truck bed for the Ford F-150 Lightning at the Ford Rouge Electric Vehicle Center in Dearborn, Mich., on Sept. 7, 2022.
Brittany Greeson for NPR
They are also, essentially, computers on wheels. Retraining auto engineers who've spent years developing expertise in gas engines and classic transmissions to now work on these new types of cars will be a major challenge that auto companies may not take on.
"For the speed that we need to move and the expertise that we need, we probably don't have the luxury of the time it will take to do all of that re-skilling," says Craig DeWald, Ford's Chief Learning Officer. "We're being strategic about going out and bringing in key talent."
Electric vehicles require millions more lines of code than their gas-powered counterparts and analysts agree few are better equipped to work on them than software engineers. Problem is, there are too few and the shortage is expected to grow to almost 1.2 million by 2026, according to the Bureau of Labor Statistics.
"There will be layoffs because there are different kinds of workers that are needed," says Michelle Krebs, executive analyst with Cox Automotive. "Software engineers are hugely important in EVs."
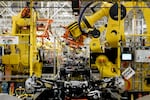
An assembly line utilizing automated machinery for assembling the Ford F-150 Lightning at the Ford Rouge Electric Vehicle Center in Dearborn, Mich., on Sept. 7, 2022.
Brittany Greeson for NPR
Trying to find talent at universities and looking farther afield
Universities that were once a reliable pipeline for talent for the U.S. auto industry have to change, too.
"Some of the larger universities are recognizing they're behind," says Ford's DeWald. "They've got to catch up and they've got their own learning to do to really sort of come along and continue to be relevant in the way the world is changing."
At the University of Michigan's auto engineering department, not a single student signed up for a course on automatic transmissions last year, a class that would have normally drawn 80 or so students just a few years ago.
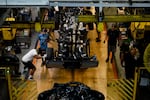
Employees work on the assembly line at the Ford Dearborn Truck Plant Final Assembly Department in Dearborn, Mich., on Sept. 7, 2022.
Brittany Greeson for NPR
The university is offering more courses central to electrification and battery-powered systems, but it's struggling to find instructors for some essential courses.
"We can't find anybody who is teaching systems engineering for software and that's the key issue," says Arthur Hyde, director of the automotive engineering program at the University of Michigan.
Both universities and companies are addressing this vexing growing by looking for talent a little farther afield. A growing number of students in Hyde's classes are from China and India, a talent pool U.S. automakers are also tapping into.
"Most companies I'm aware of have engineering centers in India that do nothing but write software," says Hyde, who's a former Ford engineer. "It's like an assembly line."
‘Transformations are messy’
Gas cars are still major money makers for the auto industry. Soaring demand for Ford's new electric Lightning hasn't put a dent in sales for the classic F-150, which still roll off the assembly line every 53 seconds.
Companies will hire software engineers and gradually fire others who've long worked on gas-powered cars, as Ford did last month when it let go of 3,000 white-collar employees.
"Transformations are messy, they're ambiguous and as a part of this transformation, we have to look at everything that we do across every function," says Jennifer Waldo, Chief People and Employee Experiences Officer. "Look at Kodak. They had much of the product in the beginning and just sort of missed it. We've learned a lot from those lessons."
And so the race is on. Not simply to reach the electric future, but to find the right minds to get there.
Copyright 2022 NPR. To see more, visit https://www.npr.org.