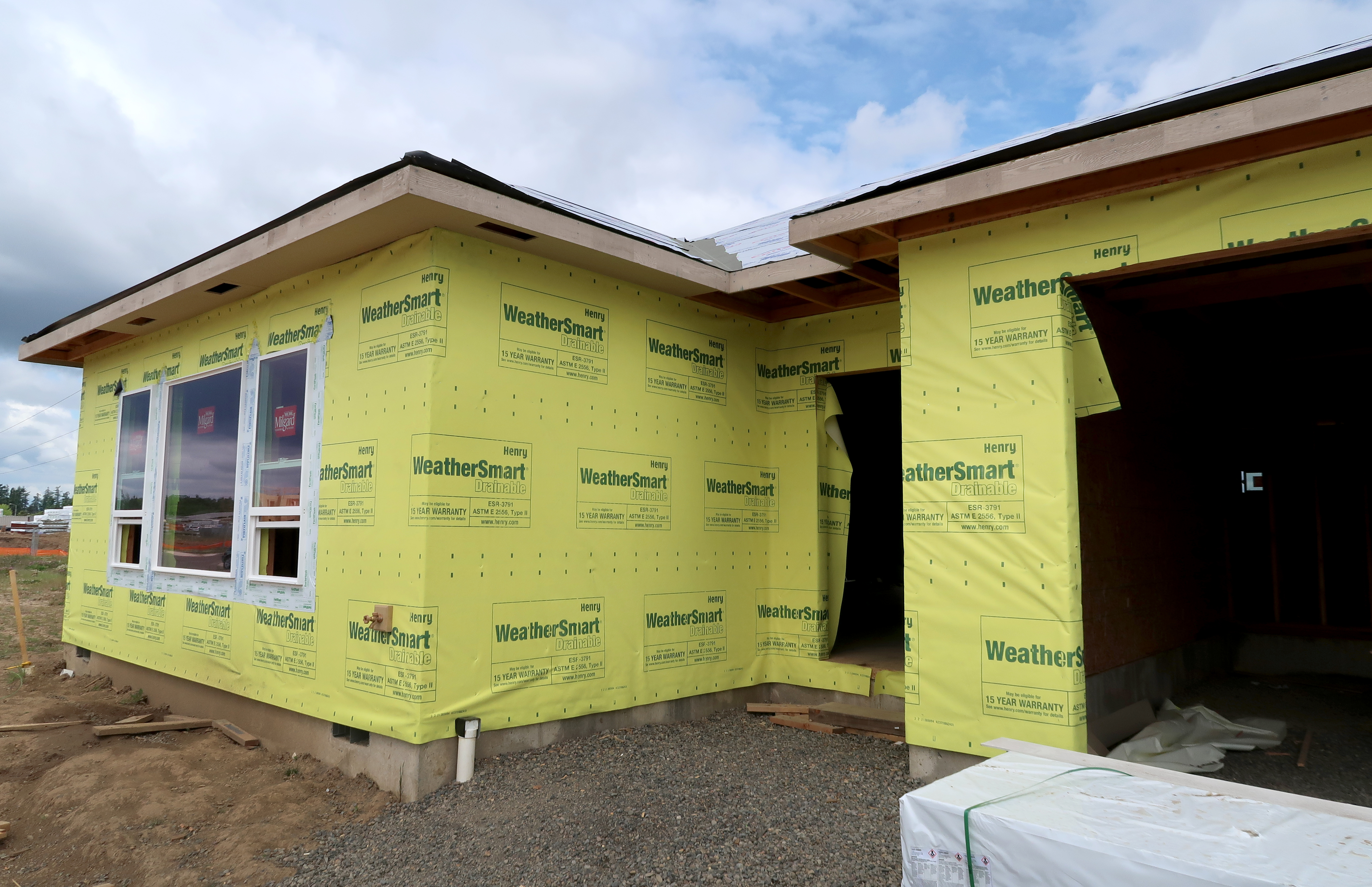
The city of John Day plans on building at least ten 3D printed homes by the end of this year, with quicker construction time compared to building a home the traditional way.
Elizabeth Miller
The city of John Day has been in decline for decades. Now, the city is trying to grow its population by 20% within 5 years. The plan is to build more homes in the community, but they won’t be doing it the old-fashioned way. The city plans on 3D printing homes with concrete and aims to construct at least 10 homes by the end of this year. We’ll hear from City Manager of John Day Nick Green on his hopes for the city that 3D printed homes will bring.
The following transcript was created by a computer and edited by a volunteer.
Dave Miller: From the Gert Boyle studio at OPB, this is Think Out Loud. I’m Dave Miller. The city of John Day has plans to print some new homes. You heard that right. The city wants to use a 3D printer to build at least 10 new homes by the end of this summer. Nick Green is the city manager of John Day and he joins us now with the details. Nick Green, welcome to Think Out Loud.
Nick Green: Thanks Dave. I appreciate you having me on your show.
Miller: What is a 3D printed home?
Green: It’s fascinating technology but I also want to demystify it a little bit. At the end of the day it’s just concrete. It’s concrete walls, interior and exterior, built on a concrete foundation. What’s unique about it is the way it’s delivered. So it’s a special formula that comes out of essentially a robot that’s operated on a platform and it can print continuously layer after layer with whichever type of design you enter into the system.
Miller: Meaning it’s highly customizable. You program it to squirt the concrete as it moves along some grid and you can make any shapes you want.
Green: Exactly. And right now there’s only a handful of companies in the country that are experimenting with this and so they’re looking at different types of formulas and different methods for delivering that through the 3D printed nozzles. But the potential is you can print, you’re not constrained to squares and rectangles. You could do single story, two story, cottage cluster, duplex, triplex, flat ground or sloped. So we’re experimenting with all of those configurations in the design that we’re looking at for John Day.
Miller: How long does it take to print a house, say to print a duplex?
Green: I think that’s the beauty of the system is you could actually print overnight. You can have a complete home erected within about a day or two, because the printer doesn’t need rest, it doesn’t have to take breaks. As long as you keep your formula coming, it will continue to operate.
Miller: We’re not just talking about exterior walls. We’re talking about internal walls as well, instead of a stick built home with studs and drywall?
Green: Correct, both the exterior and interior walls can be printed with interstitial spaces that allow for insulation if you desire it or your climate warrants it as well as all the utilities that would normally be placed within the, between the drywall and a stick framed home.
Miller: How is the cost of the construction of a 3D printed home going to compare to a traditional stick built home?
Green: That’s a great question. And since I’m a public official, I’m gonna make a rare honest answer. We don’t know. If I were selling you something I’d say 15-20% less.
Miller: Well, that’s what I’ve seen. I have seen that quote from the owner of the company that you’re using. You don’t know that you can believe him right now?
Green: No, I actually do believe him. I think the challenges we have an N of 1, you know, two now that have been printed as part of their prototype development.
Miller: This is in Virginia?
Green: In Virginia. So we’re on par with Texas. I think we’ll be doing the first neighborhoods and ours is fairly small. We’re looking at 10-12 units, so cost is going to fluctuate depending on the efficiency of the setup, whether you’re doing a single family cottage cluster, which is a smaller one or two bedroom home versus a duplex or triplex where you have less material that has to be printed. So that’s going to affect cost as well as a host of other factors. But I think what we’ll see over time is you’re delivering much more efficiency because you can print them quicker. And for rural communities, it makes a lot of sense to experiment with this because we are highly labor constrained. We don’t have large scale homebuilders chomping at the bit to come to our community. It would take every contractor in the county just to build 12 houses. We average 3-4 a year, in the entire city.
Miller: This is such an interesting point because so often when I talk to elected officials or people who work in the public sector, they tout the opposite: they tout the number of jobs that they’re going to be able to create with whatever policy they are talking about. You’re saying you don’t have the jobs and so you need to accomplish this goal, building more homes without human beings actually doing that work. You don’t have the human beings.
Green: Exactly. And honestly, if we could push this down to the point where we’ve got advanced high school students designing homes and they’re part of the team that’s doing the print, that’s about the best technical training for that future career field that you could find. And I think we’d see that our 16, 17, 18 year olds have a very high aptitude for this. And it may be one mechanism, that skilled training in high school that helps us address labor shortages in the market as our workforce and population ages.
Miller: But why are you doing this to begin with? I mean, we started with the technology because it is sort of the exciting aspect of this. But why does the city of John Day need to even be in the business of building homes to begin with?
Green: Well, it’s a good question. So, we’re doing this as a public-private partnership. The city is investing in the design in partnership with the Department of Land Conservation and Development. We’re working with the Ford family through a new program called Growing Rural Oregon, Business Oregon. There’s a variety of public agencies that are invested in this. The homes themselves are going to be privately owned and operated, the city will not own the housing and the contractor that’s building the housing is a private contractor who alchemists will be subcontracted to. So we’re using a P3 approach, public-private partnership, to incentivize home production at a scale that’s simply not achievable by the public sector alone or by the private sector alone in our community.
Miller: And who are these homes going to be for, do you imagine? Obviously it’s a private sector so they could go to anyone but who are you hoping to provide homes for?
Green: The developer is Mahogany Rich Properties. It’s a veteran owned small business. And the model they want to pursue is similar to what’s been done in La Grande and Baker, which is a veteran’s village. So they want to have this first batch of homes available to honorably discharged veterans and they’re not using VA funding or any other type of federal stimulus in the mix. But they do want to give veterans preference for this housing. So that’s their target demographic. And we’re also looking at, can we create a common space or a community building that would create a sense of place and a shared environment for them to get together and really feel like they’re part of a community and not just living within four walls and under a roof?
Miller: If this works, what’s the scale of homes that you think is possible to build in John Day over the next couple of years, compared to the status quo, that the number of homes you’ve been building over the last couple of years?
Green: Our target is 100 homes over the next five years, starting in 2022. We have actually gotten all 100 homes in three different developments through the permitting process, so they’ll still need building permits, but if we can do 100 homes in five years, compared to 3-4 a year today, then you’re looking at a 20-30 times increase in housing production. And probably more importantly, we only have 800 dwelling units, so about a 20% increase in the amount of housing and also in our population, which would put us right back to where we were in the 1990s when our timber economy collapsed.
Miller: And your projections say that you can actually sustain 100 more households. There are enough jobs and services for that many more people?
Green: Absolutely. We have a tremendous number of jobs available currently. We’re targeting digital commuters, entrepreneurs, active retirees who want to live in an affordable community with quick access to a beautiful mountain environment. We think, given the increase in the price of housing and the desire to get out of some of these more congested, urbanized areas, we’ll definitely see demand for the housing and if we can get it built on that time frame, I think most of these will pre-sell, if not sell within a few weeks of being opened.
Miller: It’s interesting that you talked about back when timber was more booming as the marker of the population because the houses we’re talking about, these are they’re not going to be necessarily fully woodless, but compared to traditional, the way people build houses in most of the country, including in Oregon, this is really different. These are concrete homes. Do you feel like you’re going to have to market them or the people who actually own them, to sell them? The developers are going to have to market them differently to get people to buy into this idea of how a home is made and what’s inside it?
Green: I guess the honest answer is, I don’t know. I think what we’re seeing is a very topsy turvy housing market in Oregon and across the United States. Portland is now investing in mass timber and John Day is doing concrete. So if that doesn’t open your eyes to how dynamic this is, I don’t know what will, but I think what people really look for at the end of the day is quality. So our gold standard is communities that are mixed income where you have an opportunity to know your neighbor and you feel like you belong and have a sense of place that are attainable for your income level regardless of what that is, as well as your personal needs. And I think that’s one of the things that is often overlooked. We have an aging community, we don’t have housing that allows people to age in place. And so it creates this downward pressure as the number of people per household gets smaller over time, as families move away and you’re left with the grandparents at home, but also they want to stay in the community and they often, the home you raise your kids in isn’t the one that you need to retire in. And so we’re trying to create housing that allows people of all age groups as well as incomes to remain in the community and feel like there’s a home for them.
Miller: Nick Green, thanks for joining us today.
Green: Thank you.
Miller: Nick Green is a city manager of John Day.
Contact “Think Out Loud®”
If you’d like to comment on any of the topics in this show or suggest a topic of your own, please get in touch with us on Facebook or Twitter, send an email to thinkoutloud@opb.org, or you can leave a voicemail for us at 503-293-1983. The call-in phone number during the noon hour is 888-665-5865.