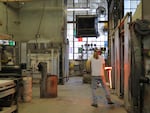
A few Uroboros workers will have the options of transferring to California to work for Oceanside. About 40 people work at Uroboros.
April Baer / OPB
2016 was the year one modest Forest Service research project turned the Northwest’s storied art glass industry upside down.
Samples taken near two Portland art glass factories were shown to carry dangerously high concentrations of heavy metals. These companies make supplies for glass artists all over the world, from stained glass church windows to fancy light fixtures in big hotels — even most the blown glass holiday ornaments you might have had hanging around the house last month.
Northwest's art glass makers are known all around the art world for their vivid colors — made with cadmium, chrome and other metals. So these makers came under intense scrutiny from their neighbors, from state regulators, and the U.S .EPA.
After a tumultuous year of regulatory and public scrutiny, Eric Lovell is spending this winter preparing to send his 44-year-old art glass business, Uroboros Glass, into new hands.
Lovell made the decision this fall to retire and sell his business to a California-based company, Oceanside GlassTile. While the company has some Oregon connections, it means the loss of some 40 Portland-area jobs to Oceanside, whose production facilities are in Tijuana, Mexico.
Lovell showed us around the plant, which is wrapping up a few last orders before moving equipment and sending formulas to Oceanside.
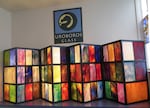
April Baer / OPB
“This building was built in 1924,” Lovell told us, over the roar of furnaces and filtering equipment. “It’s almost 100 years old now. It was built by TrusCon Steel for the the purpose of making steel windows — like the building is made out of. It’s an entirely glass-walled building. They operated here up till World War II. We moved in, in the early '80s."
Lovell started the business in 1973, and the plant in Northeast Portland is Uroboros’ third location.
Q&A with Eric Lovell, President, Uroboros Glass
April Baer: What did it mean to be able to move into a space like this?
Eric Lovell: Well, it was a huge step for me at that time. It was five times the amount of space we had in our previous place, in close-in Southeast, yet it enabled us to go to a faster annealing process and cover the volume we anticipated. We actually subleased part of the building for about ten years and didn't fill it up ourselves until the early '90s. Uroboros is what I call a high-mix, low-volume manufacturer. We make a large variety of very small quantities of things. So basically you're looking at an open warehouse here. The melting and forming equipment is in the far end. The glass is coming through the annealing layer, it takes about an hour transit time to go in there and cool off.
We selected this building originally, partly for location and size, but partly because it had a lot of daylight. And for stained glass artists, that was our primary business when we moved in here, being able to see the glass the way it would normally be displayed in a window, the light quality is important. That's worked out really well for us.
Baer: What was your own process of exploring what color?
Lovell: It was a tremendously creative period. I was driven by what the customers wanted to get from the glass. They wanted deep leafy greens with rough textures that mimic nature. So I'd try to make a deep leafy green. I'd go into the forest and just stare at hillsides covered with trees to look at green mixes. If they wanted a sky glass you try to put together a light gray-blue, with just hints of blush pink to make a glass that could be used as a sky in the background and water — different kinds of textures for water than for a leaf or a flower. That was the driving factor there. So trying to make the glass look like that was the challenge at that point.
Baer: Going back a year when the U.S. Forest Service moss study first surfaced, kicking off a storm of public interest in glass making and toxics, did you have a sense of what the study was going to mean?
Lovell: I certainly didn't. I didn't know anything about moss samples. Certainly learned a lot about it since then. There were so many other issues coming down at the same time, as a result of DEQ and the governor's actions that it was all wrapped up into a big complicated mess.
Baer: What were some of the other pressures coming to a head at that time?
Lovell: Well, of course we had DEQ and its move to make restrictions on all glass makers without any evidence from any emissions from most of us.
Baer: To be clear, you felt the link was never demonstrated between the moss and what is made here?
Lovell: Oh, it certainly wasn't. A piece of moss can be contaminated by something very limited and local around them. There's other moss samples on the other side of the freeway the same distance from us as the one sample they associated with us and they didn't have high cadmium in them. In my view, it was never demonstrated we had anything to do with that moss sample. It was pure hysteria in the part of the media and unfamiliarity with the information from the Forest Service and the DEQ. They didn't know what to do with moss samples either.
Baer: What were some other pressures on the business at the time?
Lovell: Because of the news, every regulatory authority Oregon has, I think, came through and inspected us. It's really not part of the story I want to get into here. But those things happened.
Baer: What was the decision process you found yourself going through?
Lovell: Partly my age, partly the ramifications of the new regulations for emissions, and seismic and fire, adding to the complexity of being a business of this size. These regulations are one-size-fits-all, the same for a nuclear power plant or the Hermiston coal-fired power plant. They take a tremendous amount of management oversight to comply with, with thousands of dollars of fines per day, if any one of your employees makes a mistake. I'm too old for that stuff. That's not why I got involved making art glass for artists. If we were a bigger company and had enough revenues to support a regulatory compliance position, we might have been able to absorb the costs. But we're in a scale kind of in between a one-person, fly-under-the-radar garage and a utility. Those factors, the increasing gentrification of this neighborhood is certainly a factor. Light industrial means a different thing than it did 32 years ago.
Baer: For those who don’t know this part of town, who’s moving in?
Lovell: There are small scale makers, designers, fabric artists. There are people living in the warehouses around us, against code. What used to be primarily a manufacturing and warehouse neighborhood devoid of people except us is now busy and thriving.
Baer: It sounds like it wasn’t just a matter of having enough money for baghouses
Lovell: Oh yeah. Installing the baghouses is a relatively easy cost calculus. But there are other aspects of owning and maintaining a baghouse that DEQ has insisted on.
Baer: Oceanside GlassTile, a California company, has agreed top purchase Uroboros’ equipment, formulas, processes. How did the sale evolve?
Lovell: They'd already made a move to acquire Spectrum Glass out of the Seattle area, as they were a big customer of Spectrum's products and wanted to secure their source of supply. We've always had a product in common, the System 96 fusible product. I developed the name System 96 and the product with their previous owners. I think Oceanside, when they found out we were going to close, decided this was a once-in-a-lifetime opportunity to absorb the rest of System 96 production and other products that are iconic from Uroboros. I think they see the collaborative benefits of having these all under one roof. I'm really excited by that. I'm looking forward to working with Brandon Bhyre [the Vice-President of Operations] from Spectrum and seeing what we can do with having what we all know about working for a common cause and product line.
Baer: Were there other suitors for the company?
Lovell: Yes, there were. No serious ones in state. There were some Looky-Loos in Oregon. I had one serious suitor from a Rust Belt city and a pretty serious one from Europe.
Baer: There’s a relationship with Oceanside in that [Bullseye Glass co-founder] Boyce Lundstrom, who you know from back in the day, is also the co-founder of Oceanside. His nephew, Sean Gildea, now runs the company, right?
Lovell: Absolutely. One of my criteria in working with candidates was to fund people who had a good aesthetic understanding of the products and the marketplace, and a strong environmental commitment, keeping a really positive and supportive relationship with the staff. These guys have proven to me they have all those aspects in their business culture. To me that seemed like a good home for what Uroboros means to its market and to me.
Baer: A number of glass artists have noted with Spectrum and Uroboros shutting down, domestically-made glass will now be fabricated at Oceanside’s Mexican operations in Tijuana.
Lovell: I would have preferred to have it stay here in Portland. At least in the Pacific Northwest. The further it gets away, the less happy I am. But I can't overlook this was the one best opportunity we had to sell the company. They are professional glass makers already. it's a much cleaner and newer plant than we have here. They employ a lot of people in California too. It makes sense and it's the best option we have.
Baer: Some artists are concerned about what’s going to happen to the price of products like Spectrum 96 [with production concentrated out of state].
Lovell: I think they have to calculate what their costs are going to be. I won't be in control of pricing. Obviously they don't want to price it so high they price themselves out of the market. Conversely, they don't want to price it so low they don't make this investment worthwhile. I was making predictions based on the cost of new regulations it would cost about 15 percent more for whoever made a move to comply.
Baer: Will staff at Uroboros will be losing jobs in 2017?
Lovell: That's really the saddest part for me. Our average tenure here is about 10 1/2 years. I have several people with over 20 years of experience. I'm working with all of them to transition to different positions. There's opportunity for some positions to relocate to San Diego. Some staff will work on a short-term basis for several months to get the new production facility up and running. Other ones, we've had some departures already as people fund jobs. We're looking to place each one of them. We've employed four people who were developmentally disabled, doing packing and simple jobs at this time last year. We still have two here now. They're very hard to find positions for. We're doing what we can to get them placed in an equivalent or better job.
Baer: What does it mean to pack up this place, which has been the work of your life?
Lovell: There have been a lot of stages of sorrow. I've spent my whole life creating things — product or machines or tools or jigs. It's the opposite to be disassembling them. Personally I'm thrilled to know there are people who will pick up the pieces and put it back together and make it work right again. But for all of us, it's death by a thousand cuts. Every little disconnect is one thing that is going away. It's definitely going to be a strange feeling to be in the building this summer when it's handing out.
Baer: Prior to 2016 had you thought about selling the business?
Lovell: Yeah, I had been preparing to sell for some time, preparing for my own retirement. It's a complex enough business I didn't want to be running it myself as I aged, particularly with he complexities of the new regulatory environment. That's a little bit more than I wanted to be worrying about on a day-to-day basis. I had been entertaining offers to buy the business and run it in-site before 2016. One of those withered pretty quickly when the news came out about glass makers in Oregon. But that was on the horizon. You have to have a succession plan. I'd told friends for several years my greatest professional goal at the time was to find a way for Uroboros to continue without me.
Baer: Do you think you could have done it?
Lovell: Yeah. I think I could have done so.
Baer: It’s been hard for the layperson to get their heads around what happened. I think the perception was that the glass industry was unregulated. It’s also clear people in the industry were paying a great deal of attention to systems within their buildings. Substances like cadmium and arsenic were not taken lightly or handled lightly. What do you say to people who’ve been asking you how to make sense of all this?
Lovell: Well, that's such a long story. We here have taken many steps over the years to decrease our impact on the environment, whether it's sound on our neighbors to our recycle quantity in relation to our garbage quantity, water conservation — hundreds of steps in manufacturing to our general business practices. We used to design our packaging with white cardboard boxes with colored print. We went to brown cardboard boxes to avoid the bleaching of the cardboard. That cost money. We did that 15-20 years ago. So many decisions like that taken over time that were with the environment in mind. It's more than a little ironic that we, being the players that we were, got caught up in an environmental issue, compared to some of our competitors nationally, that have, to my view, not taken those kinds of steps. The Oregon glass makers have been much cleaner glass makers than some of our other competitors in the United States. It's odd that we're the ones that have gotten skewered in the news.
Baer: What have you been hearing from artists as you’ve been wrapping up operations?
Lovell: Well, like with our staff it's been a bittersweet scenario. They were really miserable when we announced our closure. They were worried about their source of supply when we were restricted overnight by DEQ from so many raw materials, and relief and joy finding out that we did have a future after we were able to make a public announcement about the acquisition by Oceanside. There's been a lot of support — people very upset with the scenario that put us in that situation. Most of the customer base feels it's very unfair, even though they don't know the details of it. I think all of us here feel a sense of pride in involved in some of the world class art projects that we have been, whether it's helping restore a major Tiffany original panel to some of the huge public works that have happened in art glass around the world. It's one of the true satisfiers of our business, to see what we worked so hard to make, used in such an artistic way.
Baer: What will you do when the transition is done?
Lovell: I really haven't thought much about he future after this. I've been so busy with the sale and the closure process. I know I'll be involved with glass. I'll be consulting with Oceanside for years to come to make sure the production is what it was originally intended to be, and help them develop new products. It really is the end of a chapter for the Pacific Northwest and for Portland, too. It's above my pay grade to understand the drivers and ramifications of all that. I think it's a shame. I think Oregon and Pacific Northwest had a unique position in the world of art glass, even though it's a very small segment of society and invisible to most of the public, it is very visible to the art glass world. It will take years to assess the ramifications of that change. But it has changed. And it'll never be the same. I think the art glass world is just seeing the very first pages of a new chapter where this collaborative company that's brought together Oceanside skills and Spectrum skills and Uroboros skills into one roof. I don't think any of us know where that's going to go. All of us on the inside of this process are really thrilled to think about the possibilities here.